See how a woodworking firm uses incident statistics to educate staff and focus the prevention efforts of their health and safety committee.
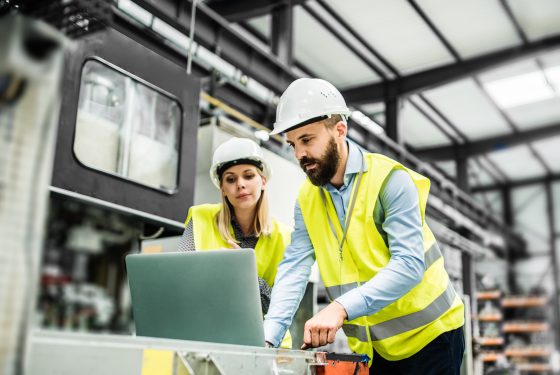
Photo credit: istock.com/Halfpoint
Dennis Trill is the production manager at Towne Millwork — an architectural woodworking firm that creates custom designs for hospitals, banks, schools, stadiums, and other commercial buildings throughout North America.
In 2004, Dennis found that 68 percent of all injuries at their Abbotsford location involved utility knives. That statistic stood out to him and he realized they had a safety issue. He shared the information with workers, and the company reviewed best practices. The following year, there were no injuries linked with utility knives.
Every year, Dennis reviews incident statistics and summarizes them in a one-page report. He shares it with the 47 shop workers and 20 office staff. He adds that it’s important to educate staff and make them aware of hazards in the workplace. About the incident statistics report: “It’s really valuable for prevention. It’s probably one of the best things that I could have ever done in the 33 years that I’ve worked here.”
Dennis is part of the safety committee at work. “As the safety committee, we’re looking, obviously, to see which incidents are trending upward. Then we’ll focus on that for a few months and give crew talks in our small huddles that we have,” he says. (See my post Tips for effective safety meetings for ideas on how to make the most of your safety meetings, so workers learn and retain health and safety information.)
How can you do this type of summary at your workplace?
I asked Dennis for his advice to other employers.
“Get all your first aid treatment records that you had throughout the year. Then go through them all and categorize them based on what pertains to your industry. Keep it simple, so that anybody can read it,” he says, adding that he wouldn’t include names of individual employees. “You don’t want to pick on them in front of all the staff. That’s not productive.”
In addition to looking at first aid records, it’s important to investigate near misses. In my post What can we learn about near misses?, a supervisor on a construction site told me that when a near miss happens, they find that some or all the risk-control steps had not been taken. A manager at WorkSafeBC agreed that it’s important to investigate and learn from near misses to prevent more serious incidents in future.
More information about risk management
See WorkSafeBC’s Assessing Risks for more information on how to identify the hazards that exist in your workplace and how they may put your workers at risk. Additional information and resources are available from the Manufacturing Safety Alliance of BC (MSABC).
Kudos to Dennis and his team for showing such a good example of safety leadership.