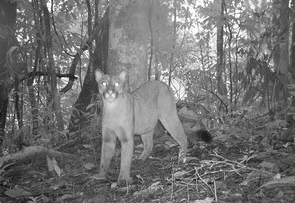
Photo credit: Smithsonian Wild on Flickr
Stalked by a cougar, cut finger while putting knife back into its casing, eye-full of mud, twisted ankle, knee bashed on a rock – these are some of the things recently shared in a “learnings database” on the intranet of Golder Associates, an engineering firm with 6,000 employees worldwide.
Everyone is encouraged to add learnings – and the goal is for each employee to add at least three learnings per year, said archaeologist Olivia Donaher, the health, safety and environment rep for Golder’s socio-cultural department in BC.
“I think it’s a great system and we have good participation on it. It acts as a great reminder to keep health and safety at the forefront of our lives and work,” Olivia said. “It’s also very useful for tracking follow-up on incidents and making sure proper attention has been given to each incident based on the risk register. Lastly, it makes the locating and sharing of incidents much easier.”
She said field workers tend to add the most learnings, but all are encouraged to contribute.
“They have made a bit of a competition out of it to encourage participation by having the department with the most learnings at the end of the year win a prize,” Olivia said.
How it works
An employee goes online to the Add A Learning pages and chooses one of the following categories: Injury/illness; Environmental incident; Near miss; and Commendation. They share the time, location, any property damage reports, and other relevant information – along with the names of the project manager and supervisor.
Workers save their input, and a copy of the learning is sent automatically to them and to their project manager and supervisor.
“The project manager then follows up and does a report of his/her own and ‘closes’ the learning, though it is always listed for reference,” Olivia said. “The learnings are sent out to each group’s Health, Safety and Environment rep each month. We discuss these at our health and safety meetings for general information, and the health and safety rep reports them at the group department meeting as well.”
It’s impressive to see a system that collects info this way and then shares it with all the right people who will make decisions about it. Thanks to Olivia for telling me more – and please let me know about any such systems you are using.
Collins Safety Services Ltd. develops and provides clients with “Online” Occupational Health and Safety Programs allowing them to expand and grow their safety management systems like never before. Having their safety program “Online” ultimately provides for better safety communication, makes information MORE accessible to everyone, and provides not only supervisors and personnel on site …but practically anyone with direct access to the required information in just a few clicks.
The response has been amazing…check it out for yourself. http://www.collinssafety.ca/OnlinePrograms.html
All the Best!