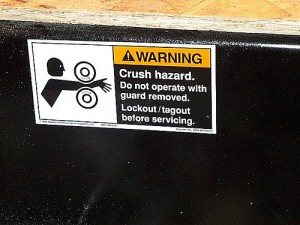
Image credit: GCPLearning on Flickr
A 41-year-old man in England was seriously injured – but thankfully survived – after he was pulled into the unguarded, rotating parts of a machine.
It gave me shivers to read the story in the Health and Safety Executive blog about Adrian Taylor, a worker in the West Midlands – father of two, same age as my brother.
Adrian had been adjusting the rollers on a machine that makes metal shelving components from steel coil. The machine started accidentally and his high-viz vest and jacket were sucked into the rollers.
“He was pulled forward into the machinery and sustained a number of injuries including a cut to the back of his head, cuts above his right eye and on his back, a swollen cheek bone, bruises on his right arm and a puncture hole in his right elbow,” reads the HSE post.
“HSE’s investigation into the incident found that a fixed guard, which would have protected workers from dangerous parts of the machine, had been removed at least two to three years previously.”
Importance of lock-out
Adrian’s story underscores the importance of lockout – defined in BC’s OHS Regulation as: “the use of a lock or locks to render machinery or equipment inoperable or to isolate an energy source in accordance with a written procedure.”
In other words, lockout stops a machine from starting by accident. WorkSafeBC is producing some new resources on lockout for manufacturers, and they already have lots of lockout resources for many other industries that use big machines – kitchen choppers, meat grinders, drilling rig hammers, dump trucks, punch presses, and lots of other things that shouldn’t turn on while you are adjusting them!
Here are more resources on lockout – and if you have any to add, please share them in the Comments section below.
Lockout a booklet from WorkSafeBC
Lockout from the Industrial Accident Prevention Association
Using lockout and tagout procedures to prevent injury and death during machine maintenance, a tip sheet from NIOSH