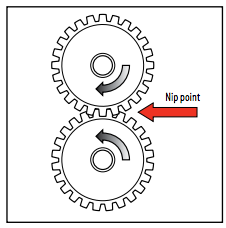
From WorkSafeBC’s Safeguarding Machinery and Equipment
Machines without proper safeguarding put workers at risk of amputation, disfigurement, and death.
“I’m often summoned in the aftermath of workplace accidents – everything from fingers torn off to people crushed in presses,” said Ian Rood, quoted in an article in WorkSafe Magazine‘s Nov/Dec 2011 issue.
Ian is the owner of UBSafe Inc., a company that specializes in safeguarding and risk assessment. He trained WorkSafeBC officers to spot and address safeguarding violations. He said that, in the past, officers tended to write up violations of lockout, when the most important issue was actually safeguarding.
“Most of the time, prior to the lockout violation, there’s a safeguarding violation,” Ian said. “The two are intertwined, but lockout is for maintenance. Safeguarding is for operation.”
An in-depth description of the differences can be found in Safeguarding Machinery and Equipment: General Requirements by WorkSafeBC.
Ian told WorkSafe Magazine that “about 70 percent of places we visited either have wildly inappropriate safeguards or the equipment isn’t safeguarded at all… This applies to everything from small shops to large assembly lines.”
Safeguarding workshop at Make it Safe Conference
Preventing machine-related injuries is the focus of Ian’s upcoming workshop, Machine Safeguarding for Tradesmen (practical and technical), at the Make it Safe Conference in Vancouver on September 21 and 22.
He said he’ll start with an explanation of BC’s regulatory requirements for safeguarding and lockout, covering the differences between production and maintenance activities. Then he’ll go into the concept of risk assessment, which, he said, “tells you, based on your level of risk faced, what the minimum acceptable level of control is.”
Ian described the outcome of his workshop, which is ideal for plant managers, operations managers, OHS managers, and others in similar roles.
“They will take away understanding of three different risk assessment models and which one fits their scenario better,” Ian said. “They won’t be able to do their own risk assessments but they’ll come away understanding the concept… It’s a good overview at the management level – the awareness level stuff that gets you on the right path.”
For more info, see Worker lost finger in wood-planing machine from the UK’s Health and Safety Executive
Machine safeguarding is probably one of the most important contributors to the safe machinery operation. And your post is a great proof of that. Also, thanks for the notification about the Make it Safe Conference in Vancouver!