BC Ferries workers use the ALERT system to report workplace safety hazards and solutions that are shared with all employees through weekly bulletins.
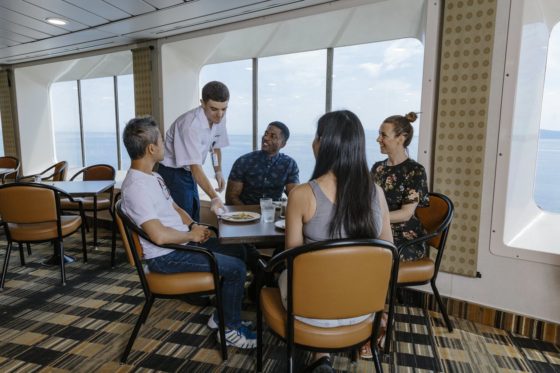
Photo credit: BC Ferries Corporation
BC Ferries employs 5,100 workers during the peak summer season. With 47 terminals, 35 ferries, and one shipyard, there are many different jobs to do. The organization’s workforce includes kitchen staff, tradespeople using heavy equipment, workers who perform marine rescues, and many more.
But no matter what their jobs are, all workers can report workplace hazards using the ALERT (All Learning Events Reported Today) system. To find out more, I contacted David Fagen, BC Ferries’ executive director of Safety, Health, and Environment.
The ALERT system encourages employees to identify hazards and take immediate corrective actions to make the hazard safe if they can. They then go to their supervisors to report the hazards and the actions they took. Employees and supervisors work together to resolve these hazards, and if they don’t find a solution, they take the ALERT item to their joint health and safety committee.
“We see it as world-class safety when the front-line employees, who are closest to the problems, can find the fixes for them,” David says. “They’re the ones who have the most creative and efficient solutions.”
Since 2008, when the system was implemented in collaboration with the BC Ferry and Marine Workers’ Union through the SailSafe initiative, BC Ferries has identified and addressed more than 8,000 hazards. BC Ferries publishes every ALERT and its solution in a weekly bulletin for all staff. The ALERTS and solutions are also used by supervisors during daily five-minute toolbox safety talks.
Examples of ALERT solutions
David shared with me an ALERT solution that addressed slippery, freshly mopped ferry decks. (Usually workers mop the decks between sailings, but they might need to mop during a sailing if, for example, someone spills a drink.)
He says: “The employees came up with a dry-mopping process. Right after you mop, you come along with a dry mop, and you basically mop behind yourself to help dry the floor more quickly.”
Another ALERT solution took place at Bella Bella’s McLoughlin Bay Terminal. Employees needed a safety solution for the mooring line they used at the dock to tie up the ferry.
“It was at an awkward angle — and really heavy and hard to manage,” David says. “It was under extreme load, and if it broke and snapped back, or something moved unexpectedly, it could have caused dismemberment or even death to one of our employees.”
In response, BC Ferries designed and installed a mooring dolphin (a floating platform that cushions a ship when it’s docked).
Read more about what BC Ferries is doing in BC Ferries programs make health and safety a daily priority for the whole crew on worksafebc.com.