Employers can get valuable information and ideas to improve safety when they engage with front-line workers through a key risk inventory.
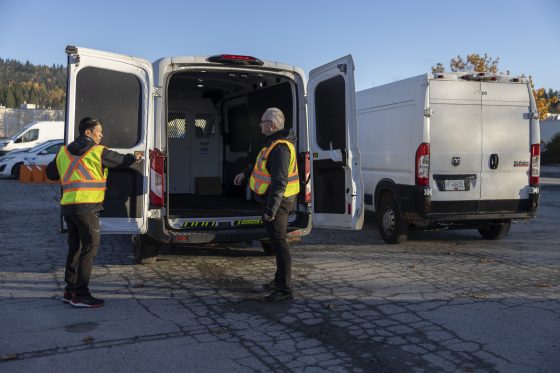
Photo credit: © WorkSafeBC (Workers’ Compensation Board of B.C.), used with permission
A key risk inventory (KRI) is a process to summarize the key risks and controls in each area of your workplace. It involves engaging with workers to identify key hazards and risks specific to their work.
Adrian Cook, a WorkSafeBC safety culture and leadership manager, describes the key risk inventory approach: “It’s an important process in identifying and managing risks in the workplace, and it strengthens health and safety culture by engaging front-line workers.”
The idea is that workers have first-hand knowledge from their experience on the job. Asking a specific series of questions often raises issues that may not already be on your safety radar. This leads naturally to an evaluation of whether the current controls are enough, and it offers an opportunity to share ideas about improvement.
Engaging workers is the first step
Recently I spoke with Stacy Purewal, a WorkSafeBC occupational health and safety consultant. Stacy coaches OHS managers on how to start conversations about workplace safety with workers, and the importance of making sure workers know that their feedback and suggestions are welcome and valued.
“Employers should listen to feedback without judgement or bias,” Stacy says. “Ask workers what they are most concerned about while they’re performing their daily tasks. Do they have any suggestions on how to better manage risks? How can we do better?”
She shows managers how to use a key risk inventory to manage risks collaboratively.
Documenting and sharing the invisible knowledge
Peter Yang, also a WorkSafeBC occupational health and safety consultant, points out that not all situations are covered in written safe work procedures.
Says Peter: “A lot of important knowledge and information is not formally documented anywhere — it’s often only known by individuals. You need to talk with workers and supervisors to get this information. Then you can identify improvements and make informed decisions that can enhance worker health and safety while increasing productivity at the same time.”
Improving overall risk management
Both Peter and Stacy have worked with employers who improved their management of workplace risks through using a KRI process.
A manufacturing employer recently discovered its workers were using a workaround whenever a critical component in the plant’s conveyor system broke down. During a KRI process, front-line workers told the employer that the work-around requires more manual inputs and introduces other hazards and risks. This naturally caused workers to be concerned about their health and safety. Peter advised the employer that a thorough planning and risk assessment process involving the workers will help identify and resolve these risks.
Stacy gives an example of another manufacturing company that implemented a safety solution suggested by workers. After a worker suffered a hand injury, the employer and workers looked more closely at the work task involved. The employer ended up reviewing its entire program for safeguarding, lockout, and de-energization. This included new written safe work procedures and training for everyone.
“I’ve enjoyed the reaction from employers when their workers share the nuances of performing tasks on the front line,” Stacy says. “Employers have used the KRI process as a catalyst to create preventative maintenance programs and to improve supervision, workplace inspections, and work area arrangements.”
Thank you to Peter and Stacy for talking with me. Visit WorkSafeBC’s webpage on managing risk for more information and resources.