A new resource makes it easier to prevent interactions between people and vehicles before they happen.
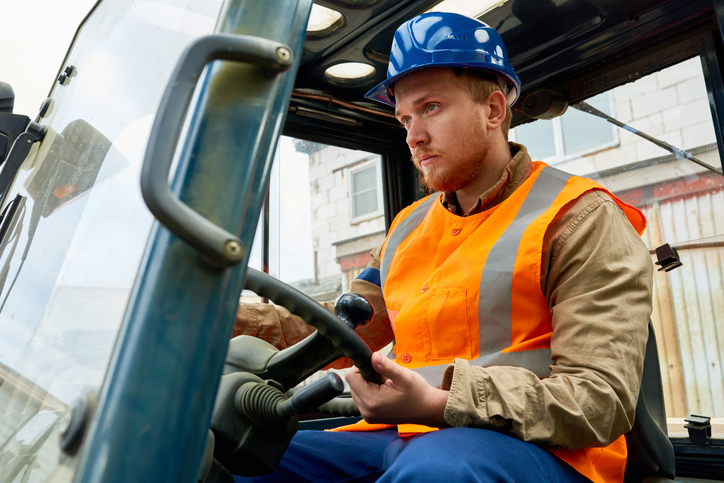
gettyimages.ca/SeventyFour
When it comes to preventing struck-by incidents at work, simply telling workers to “pay attention” is not enough says Heather Kahle, a human factors specialist at WorkSafeBC.
“We need to recognize that people can’t ‘pay attention’ to all things all the time,” Heather says. “When people are focused on their work, there is a good chance they may not notice an approaching vehicle. So then, administrative controls – such as procedures and signs – will have little influence or benefit in dynamic workplace settings to eliminate the risk of workers interfacing with vehicles.”
When a struck-by incident does happen, the results can be serious, and even fatal.
In May 2021, a young worker was fatally injured after being struck by a forklift at a wire manufacturing facility. The forklift operator did not see the worker. In October 2022, another worker was injured at a recycling depot. The worker turned around to walk in the opposite direction at the same time a forklift moved forward and struck the worker’s leg. In July 2022, a worker walking in a food and beverage warehouse was struck by a forklift backing up.
These tragic incidents are just a few of the many struck-by injuries in WorkSafeBC’s recent incident summaries. A new resource from WorkSafeBC aims to help employers prevent future incidents like these from happening again.
Planning is everything
Heather, who helped develop the new struck-by tool, says there are five primary factors which influence risk of struck-bys:
- Planning
- Equipment
- Tasks
- Environment
- People performance
“Planning and task factors play an important role in struck-by incidents. Workers may be engaged in tasks near mobile equipment which greatly increases risk,” she says. “Planning worksites – including task location, delivery and reception areas, and the general movement of people, materials and equipment — is necessary to prevent struck-bys before they happen.”
Assessing and controlling risks
The new tool includes a fillable template and a guide on how to use it. The first step walks you through how to identify all the places where mobile equipment is operating — including places that may not be top of mind. These places may include:
- Buildings
- Foot traffic areas
- Break areas
- Loading or unloading and storage zones
- Vehicle or mobile equipment travel routes
- Access or exit points
After identifying the above, employers need to engage with workers to identify and understand the tasks performed by workers in these areas. Each task description should answer the question: “Why are workers near vehicles or mobile equipment when completing this task?”
The next stage is to eliminate or minimize risk to workers. While every workplace is different, here are some of the questions to consider:
- Can some or all interactions between vehicles or mobile equipment and workers on foot be eliminated?
- Can vehicles or mobile equipment and workers on foot be separated physically or through timing to eliminate interactions?
- Can a combination of elimination, substitution, and engineering controls be used?
“The template takes a novel approach by providing a way for employers, joint health and safety committee members, or worker health and safety representatives to work together to identify and document the risk in a very visual way,” Heather says. “Visually displaying the risk can also help engage workers and leadership to solicit ideas on how to creatively and effectively prevent and reduce interactions between workers and vehicles or mobile equipment.”
Thanks to Heather for speaking of safety with me. You can read more about Controlling risks and try the tool out for yourself at worksafebc.com.