Distilleries, breweries, and wineries need to review their workplace safety measures before making hand sanitizer that helps fight the spread of COVID-19.
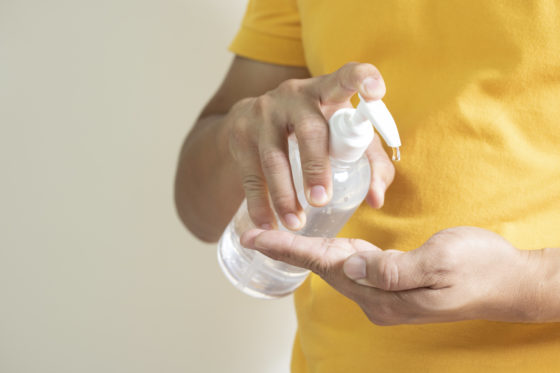
Photo credit: iStock.com/TRADOL LIMYINGCHAROENM
Recently, there’s been a lot in the news about distilleries and breweries making hand sanitizer during the COVID-19 pandemic to help with the shortage in supply. Some of the sanitizer produced is sold, but much of it is donated to front-line workers, shelters, search and rescue teams, and more. Kudos to all! Thank you for making a difference.
But pivoting operations to manufacture hand sanitizer raises some concerns from a workplace safety perspective. To find out more, I spoke with Jeanette Campbell, a senior occupational hygienist at WorkSafeBC.
Hand sanitizer requires a much higher alcohol content than beer or spirits, and also calls for chemicals not usually used in breweries, distilleries, or wineries (such as glycerin and hydrogen peroxide). This means facilities are working with higher quantities of hazardous chemicals and implementing new processes, which increases the risk of injuries, fires, or explosions.
“When you’re scaling up your production and using different chemicals you’re not familiar with, this creates new hazards. Employers need to understand what’s going on, particularly in terms of the flammable and explosive chemicals they’re using,” Jeanette says. “Do they have procedures and controls in place for protecting their workers? And what are they going to do if there’s an emergency?”
New processes call for new safety controls and procedures
WorkSafeBC staff are reaching out to workplaces that are stepping up to join the fight against COVID-19. They’re sharing a new risk advisory, Hazards in manufacturing hand sanitizer in distilleries, breweries, and wineries, which WorkSafeBC posted in April 2020. The advisory describes the potential risk and how employers can reduce the risk in their workplaces.
Employers must review the WHMIS safety data sheets (SDS) for chemicals they are using, Jeanette says. They need to know — and then communicate to their workers — the following information:
- The hazards of the products, such as flammable and explosive properties
- What precautions and personal protective equipment are required
- Where and how the products should be stored
- What to do in an emergency
Other ways employers can reduce the risk include ensuring that workers are provided with appropriate personal protective equipment, that chemicals are stored properly, and that they have documented procedures for cleaning up spills of large amounts of chemicals.
“I have huge respect for people who have come out to help solve this supply problem,” Jeanette says. “From the ones I spoke to, they’re coming from a good place in their hearts. We want to make sure that while they’re doing this great thing, they’ve got the controls in place so they can keep their workers safe as well. No one in the midst of all this wants anything bad to happen to anyone.”
For more information about safety in this industry, see WorkSafeBC’s book Health and Safety for Craft Breweries and Distilleries. To learn more about the process of making hand sanitizer, see this article from The Alchemist.
Thank you to Jeanette for speaking with me!
Very good article!